Coast to Coast
Schmitty and Sons Transportation
Location
Lakeville, MN
Industry
Transportation
Learn how Collective Data software can simplify and centralize your data—see it in action!
Assets Managed
Schmitty & Sons Increases Productivity and Reduces Costs with Fleet Management Software
About the Client
Schmitty & Sons has served their local community for over 50 years. They operate a number of divisions including school bus routing, van service, charter transportation, transit operator, and a repair and maintenance division.
The Challenge
Schmitty & Sons needed a cost-effective system that could efficiently meet their needs and accommodate the various departments and services they offer.
The Solution
By implementing Collective Data’s high-end fleet management software solution with enhanced shop management options, Schmitty & Sons has enhanced their ability to provide better, quicker service for customers. The company uses it to manage and schedule all aspects related to maintenance, parts inventory, employee records, customer management and billing.
Schmitty & Sons has taken advantage of the software’s ability to easily assign and track work within the shop. They can designate work more efficiently—the foreman can check for maintenance requests and scheduled work, open work orders, and use the work assignment view to assign work to maintenance technicians. The technicians then receive the work order with all required repairs and clock in and out with each job, which has led to greater productivity.
The software has also allowed Schmitty & Sons to make improvements in how they manage parts inventory. They’re now able to track inventory costs, as well as assign parts to specific equipment using custom reports, ultimately reducing costs.
Solution Features
- Fleet Management
- Part Days in Stock
- Work Order Part and Labor Summary
Download Our Case Study
Click here to download a sharable version of this case study.
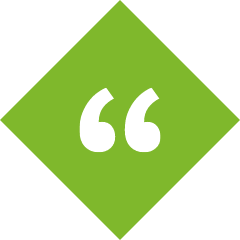
Fleet Management Case Studies
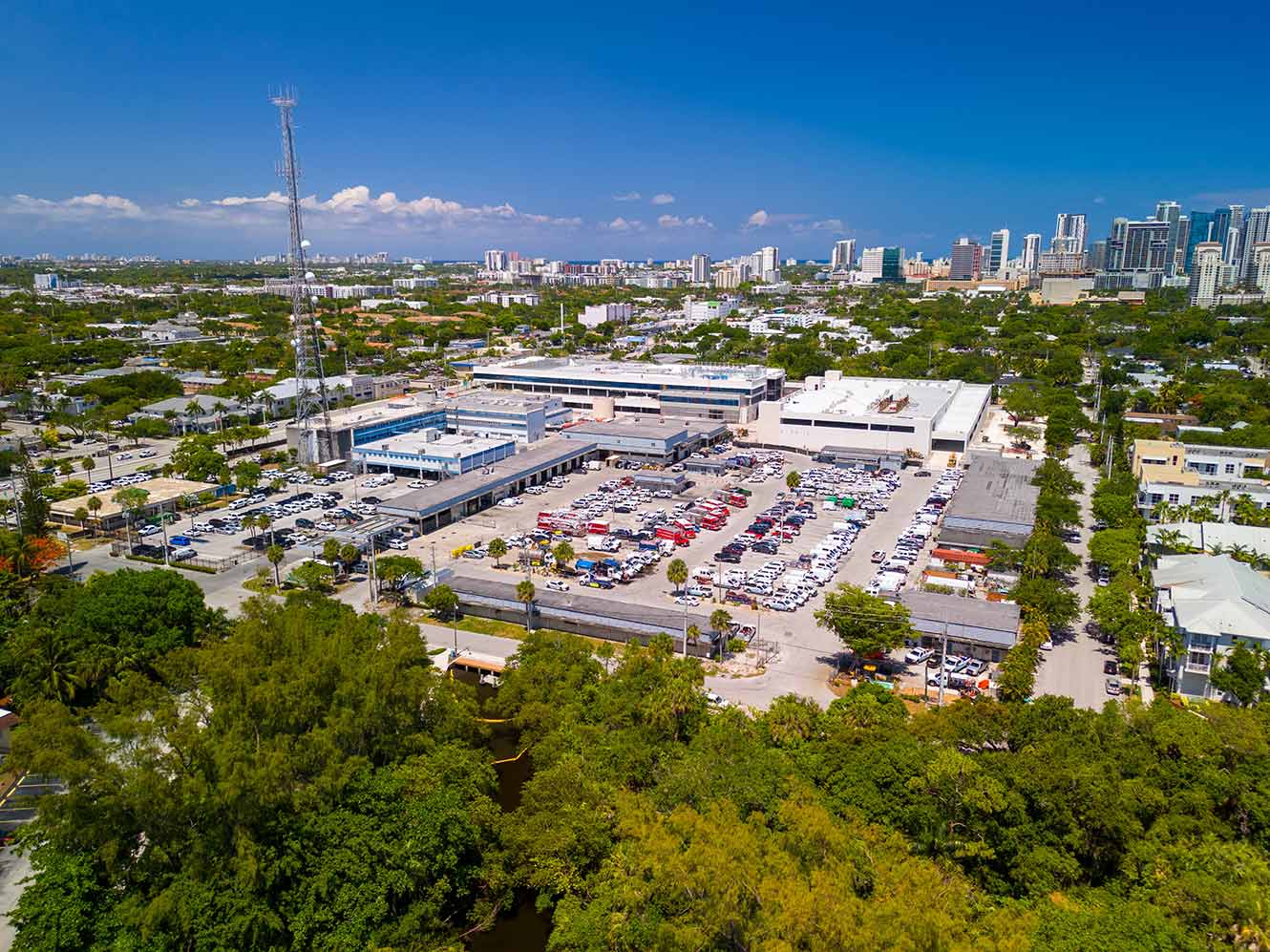
City of Fort Lauderdale
Solution: Fleet
Discover how the City of Fort Lauderdale improved asset tracking, efficiency, and accountability with Collective Data’s asset management solution.
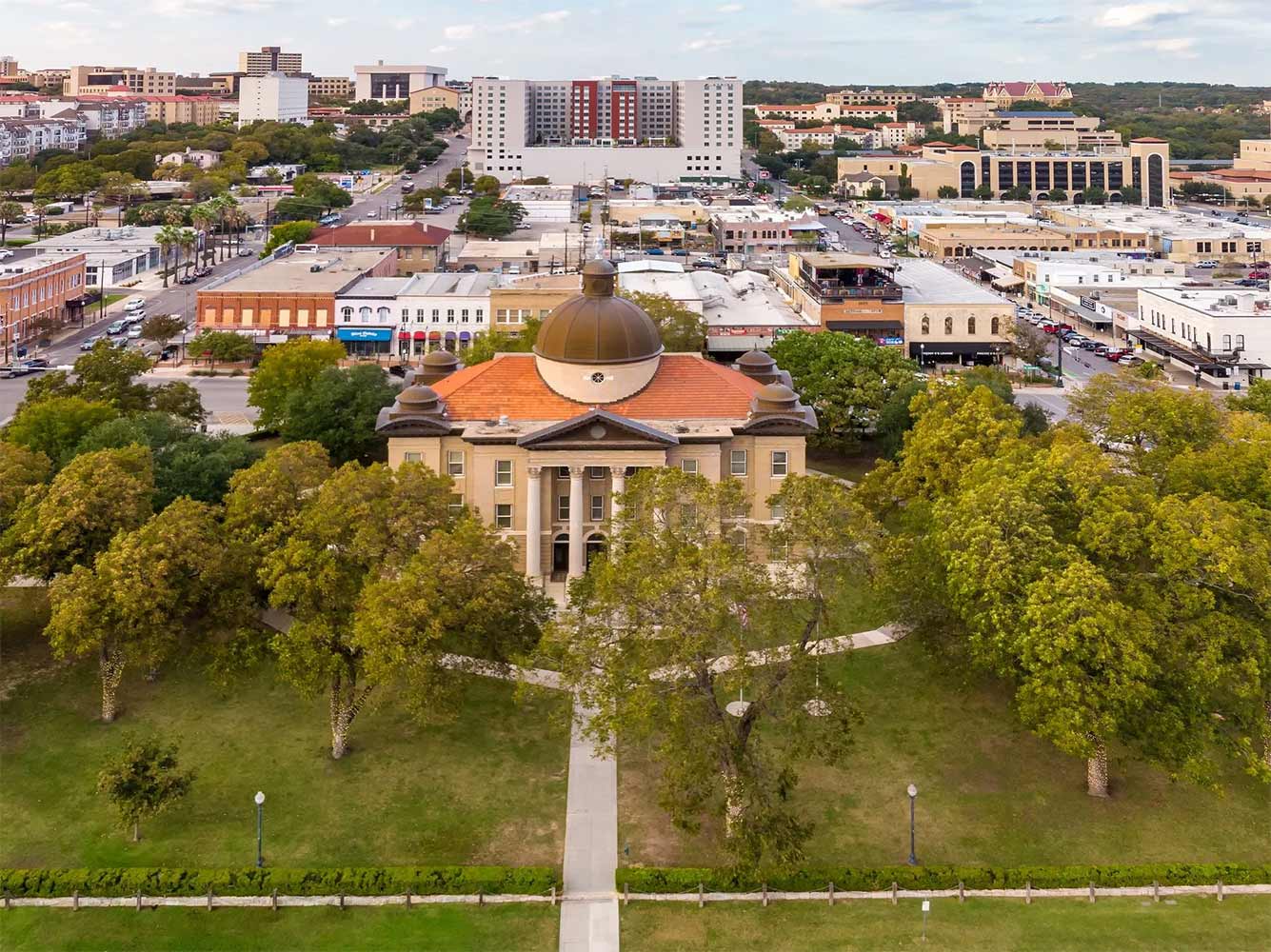
Hays County Sheriff’s Department
Solution: Fleet & Quartermaster
Hays County Sheriff’s Department streamlined its asset and fleet management with Collective Data, replacing inefficient spreadsheets with a centralized, scalable system.
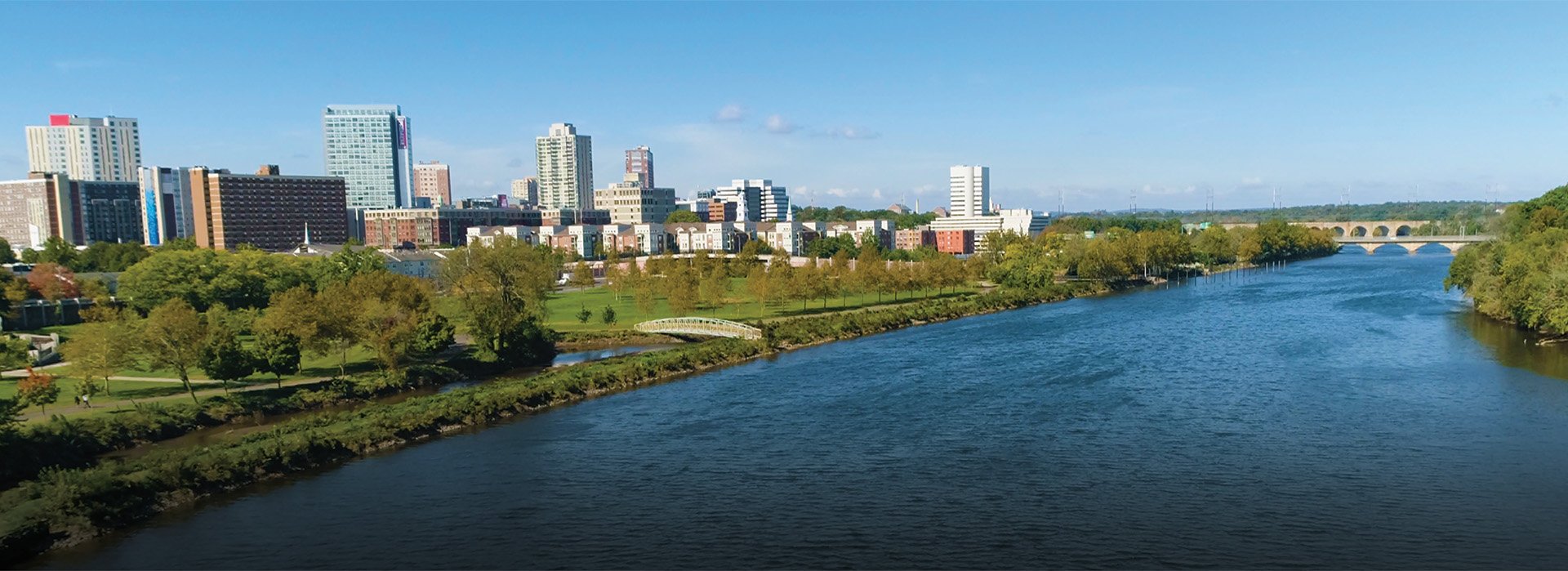
Middlesex County
Solution: Fleet
Middlesex County, a New Jersey county government, manages over 2,000 assets, including light and heavy equipment for vehicle and grounds maintenance.
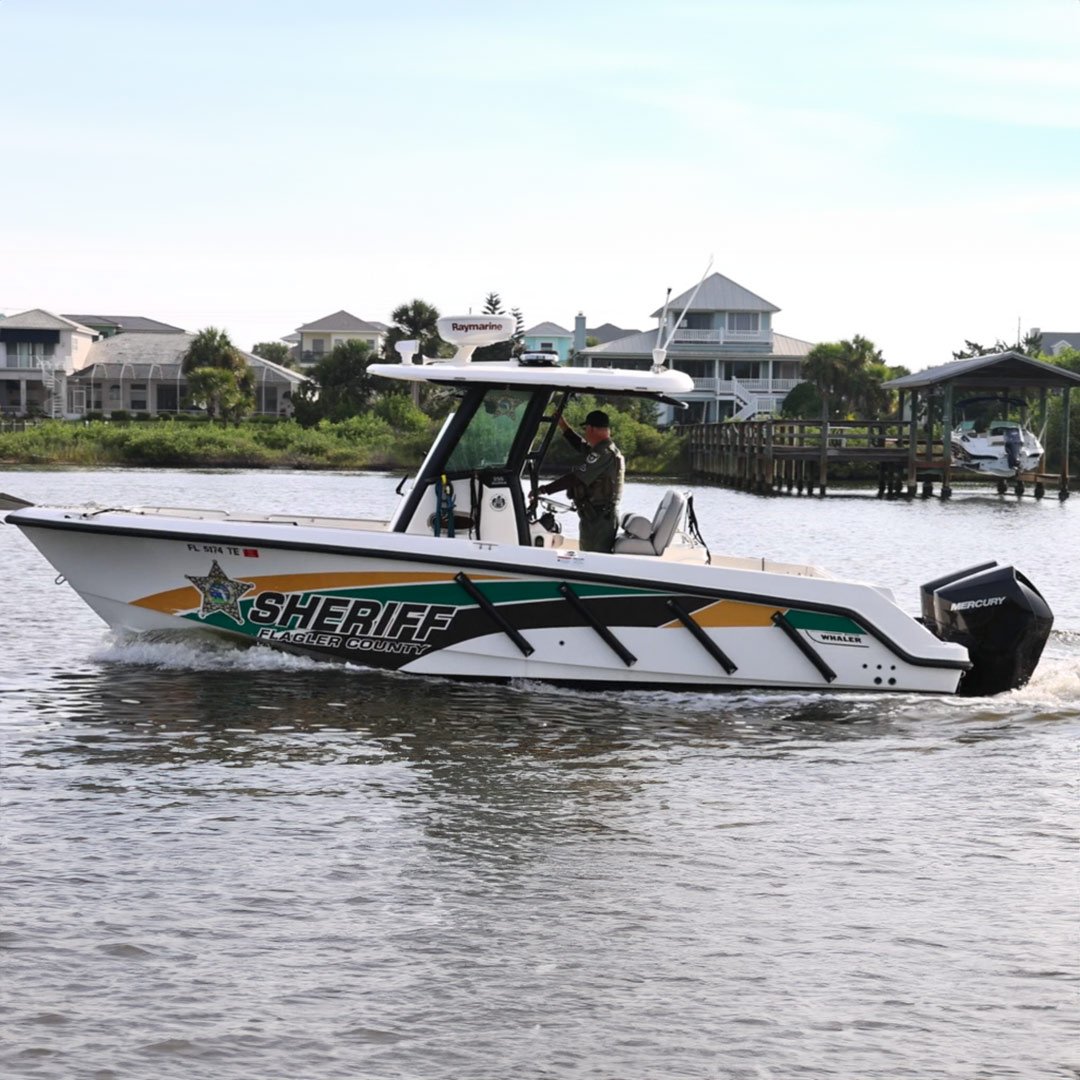
Flagler County Sheriff’s Office
Solution: Quartermaster
The Flagler County Sheriff’s Office streamlined its management of 2,000+ assets by implementing Collective Data’s system, reducing costs, improving visibility, and increasing operational efficiency with real-time tracking and customizable features.
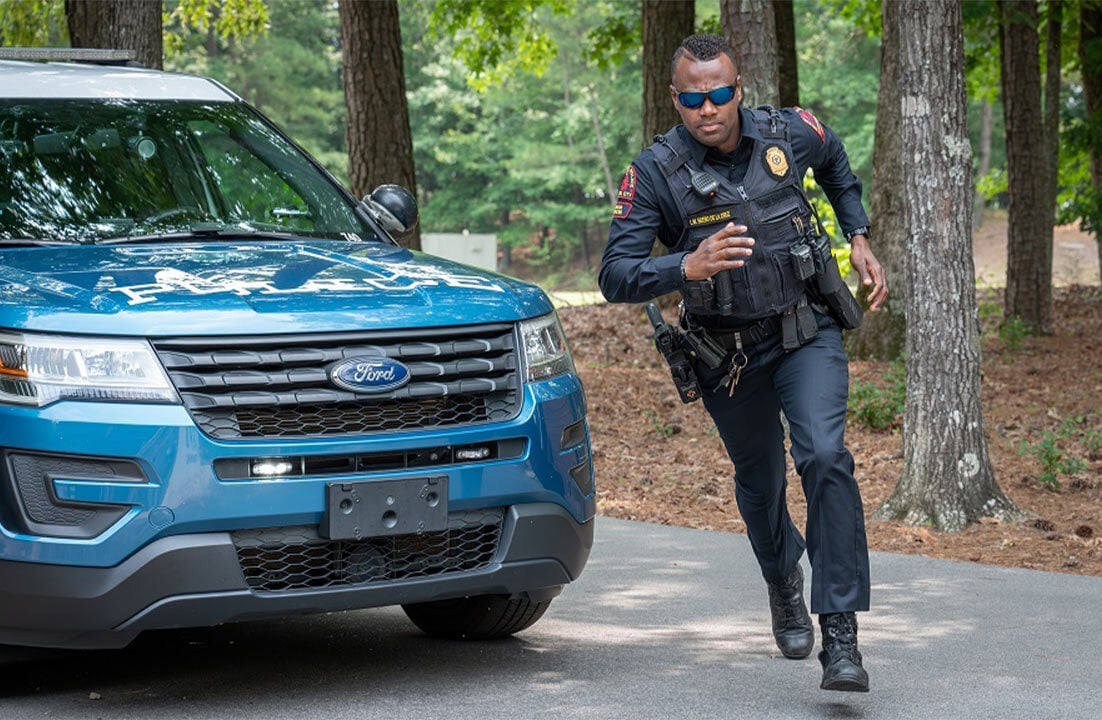
City of Raleigh Police Department
Solution: Quartermaster
The City of Raleigh Police Department manages over 1,700 assets using Collective Data’s inventory management software. This solution streamlined equipment tracking, replaced manual processes, and reduced IT oversight. According to Sr. System Administrator Brian Daniels, it has saved both time and money while improving operational efficiency and accuracy.
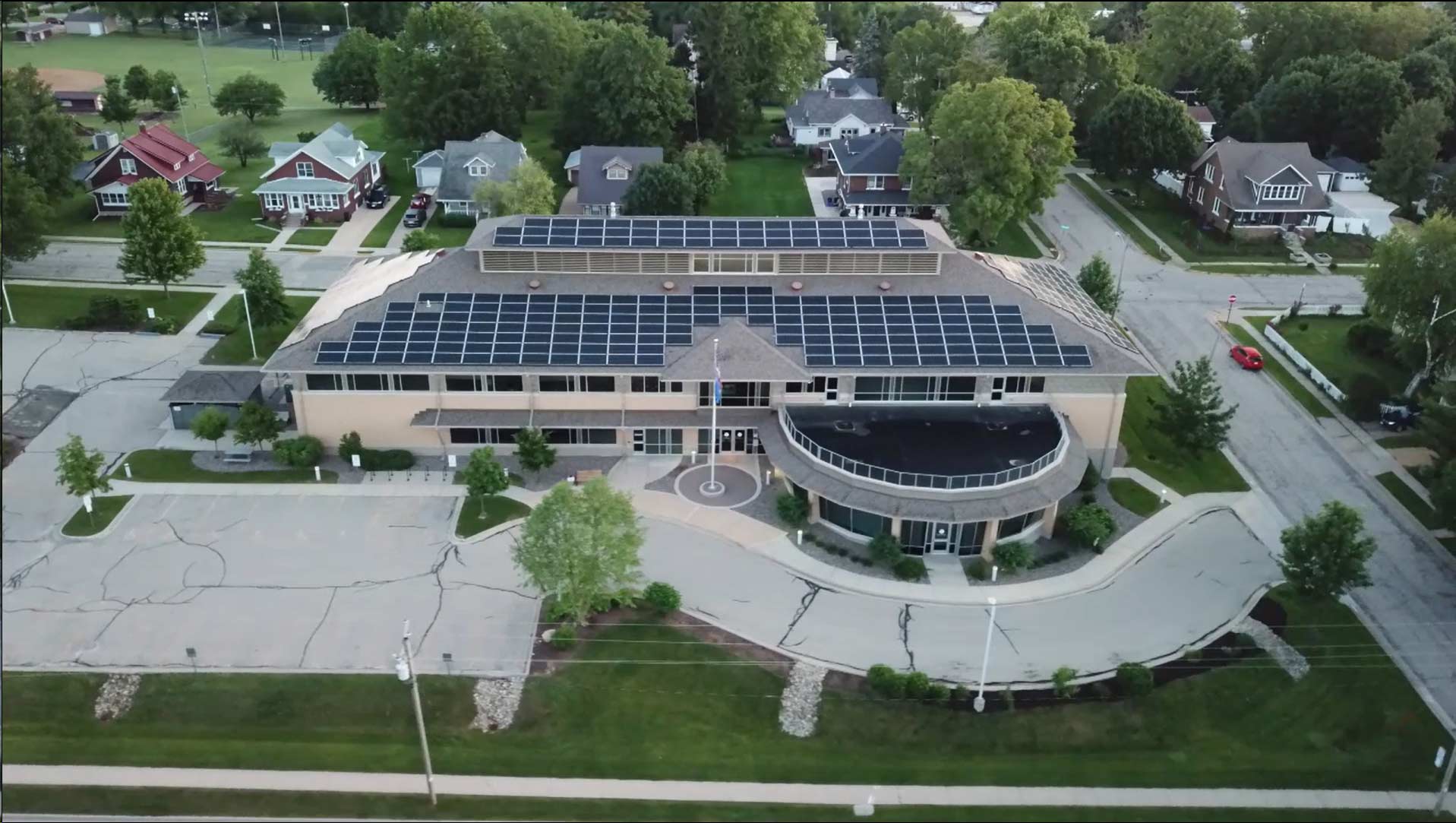
Iowa County Wisconsin
Solution: Fleet
Iowa County improved asset tracking, maintenance scheduling, and overall fleet management with Collective Data’s solution, leading to streamlined operations, enhanced reporting accuracy, and better decision-making capabilities.